図面管理システムで発注ミスを削減!製造ミスを減らすための導入方法は
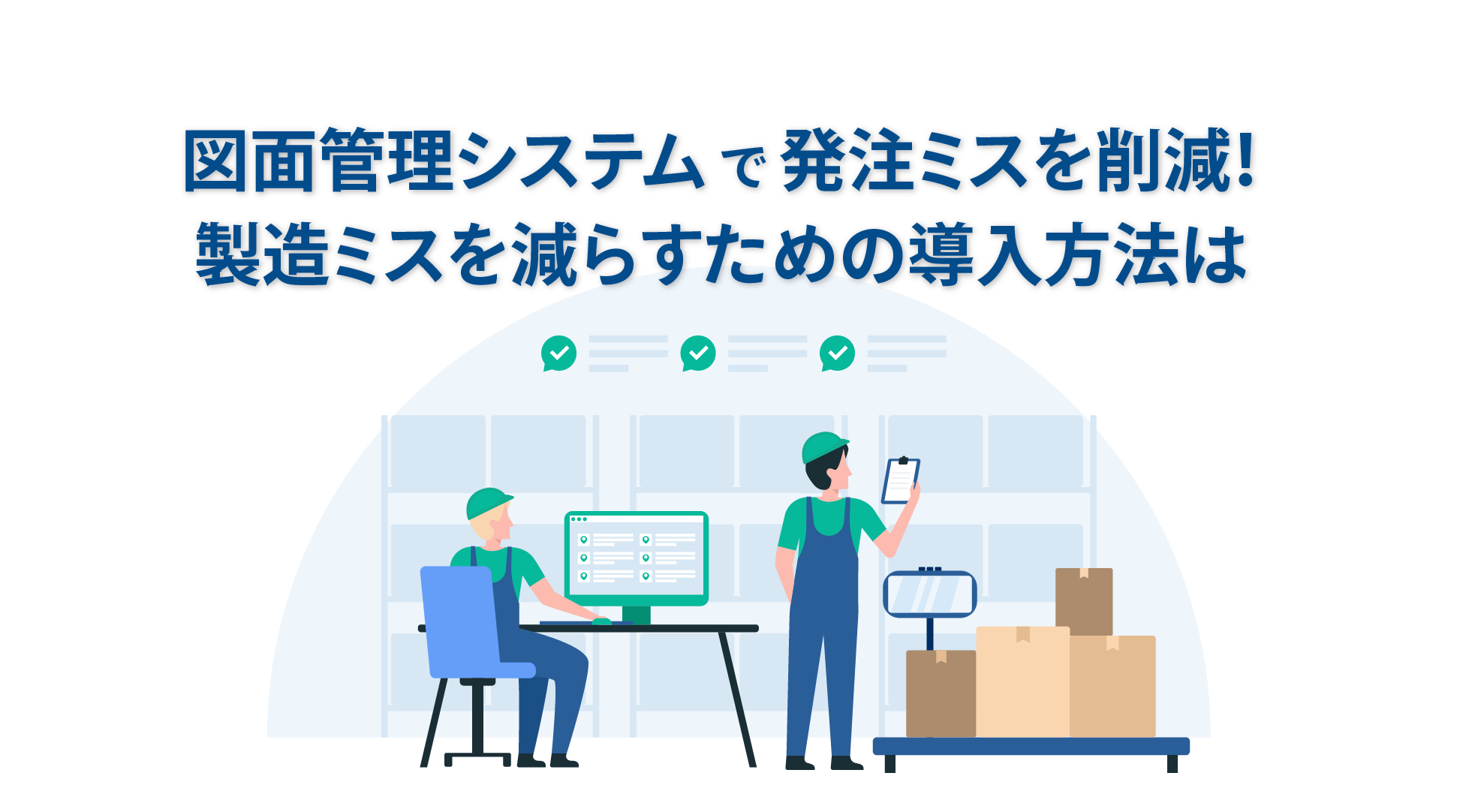
製造業において部品や材料の発注ミスは、最終的に違うものを製造してしまうなどの重大なミスにつながり、コストや納期、信頼性などに悪影響を及ぼします。
本記事では、図面管理システムと発注管理システムの連携により発注ミスのリスクを軽減する方法を紹介します。
製造業の方は、ぜひ参考にしてください。
目次
1.製造ミスを引き起こす発注ミスの原因と対策
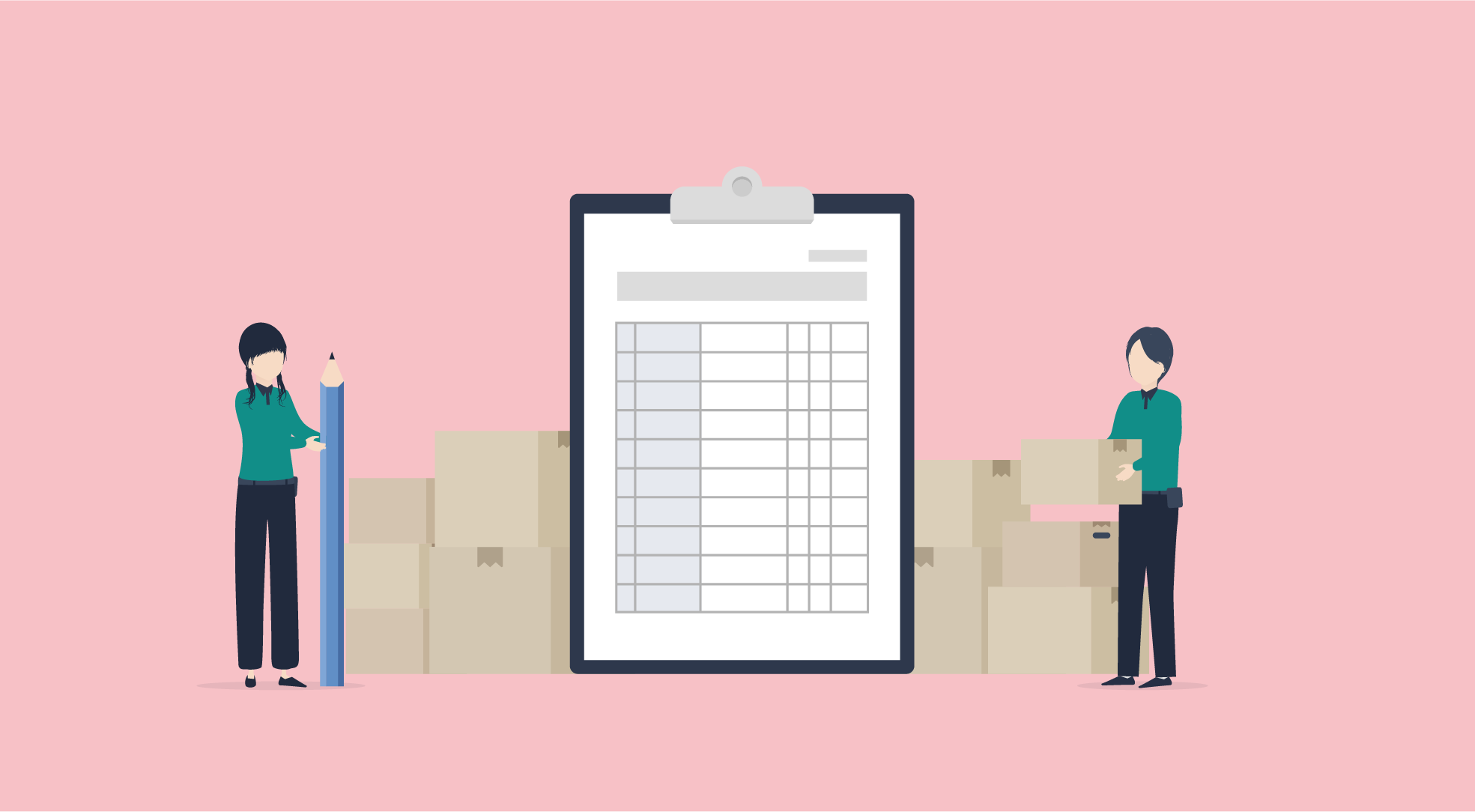
発注ミスをすると、自社や顧客にとって大きな損失となる可能性があります。しかし、発注ミスの原因と対策を知ることで、製造ミスを防げるケースがあります。
- 発注ミスが与える影響
- 発注ミスのおもな原因
- 発注ミスの対策とは?システム導入の必要性
それぞれ見ていきましょう。
1-1.発注ミスが与える影響
誤った部品や材料を発注した場合、製造ラインが停止し、製造スケジュールに遅延が発生します。また、部品の取り違えがあると、製品の品質に影響を与え、不良品の発生や、最悪の場合製品のリコールという事態もありえるでしょう。 この結果、顧客からの信頼が失われるだけでなく、修正や再製造のために莫大なコストが発生します。
さらに、従業員の労力や時間も無駄になり、全体的な生産効率が低下します。
1-2.発注ミスのおもな原因
発注ミスは原因を特定することで対策が立てられます。以下に発注ミスのおもな原因をまとめました。
発注ミスの原因 | 影響 |
---|---|
古い図面を参照してそのまま部品を発注してしまう | 必要な部品や材料が異なり、製造ミスや納期の遅れを引き起こす |
図面の改訂が関係者間で適切に共有されていない | 大規模なプロジェクトや多くの部門が関与するため、影響範囲が大きい |
見間違いや入力ミスといった単純ミス(ヒューマンエラー)を起こす | 忙しい現場や経験の浅いスタッフが多い場合に起こる。部品番号や数量違いがあると、製造ミスにつながる |
1-3.発注ミスの対策とは?システム導入の必要性
発注ミスの対策は、いかにヒューマンエラーを防ぐかに尽きます。手作業による管理は、見落としや入力ミスが起こりやすいからです。そこで、システム導入がおすすめです。
たとえば、図面管理システムを導入すると、最新の情報を一元管理され、関係者全員が同じ情報にアクセスできます。これにより、古い図面の参照や改訂情報が共有されないことが原因で、図面を取り違えるといったヒューマンエラーを防げます。
関連記事:製造業における図面管理システムの重要性とは?製造現場の役割別に徹底解説
2.図面管理システム導入でどうかわる!?発注ミス削減に与える効果
発注ミスは、図面管理システムの導入により軽減できます。ここでは、図面管理システムの概要と得られる効果を解説します。
2-1.図面管理システムの概要と機能
図面管理システムは、製造業の設計図面や設計データを一元管理するためのシステムです。 基本機能を以下にまとめました。
- 図面の登録・更新
- バージョン管理
- アクセス権限の設定
- 図面の検索機能
- 変更履歴の追跡
また、図面の共有やコメント機能を搭載しているシステムもあり、リアルタイムでのコミュニケーションを実現します。図面管理システムについてより詳しく知りたい方はこちらの記事も参考にしてください。
関連記事:図面管理システムとは?主な機能と導入するメリット
2-2. 図面管理システムが発注ミス削減に与える効果
図面管理システムは、発注ミス削減において効果的です。以下に3つのポイントをまとめました。
ポイント1:最新図面を常に参照できる
図面管理システムは、最新の図面データを一元管理します。これにより、古い図面を誤って使用するリスクが減少し、誤った部品の発注を防ぎます。
ポイント2:図面の共有が容易
全員が最新の図面情報にアクセスできるため、情報の伝達ミスや誤解を減らせます。これにより、関係者全員が共通の認識を持って作業を進められ、正確な発注が可能です。
ポイント3:ヒューマンエラーが減る
紙図面やエクセルでは見落としがちな細かな情報も、図面管理システムを使うことで確認可能です。また、チェック機能やアラート機能を活用すると、最新情報が関係者に通知されヒューマンエラーも軽減されます。これにより、誤った発注を防げます。
このように、図面管理システムは発注ミスの削減だけでなく、製造プロセス全体の業務効率化につながるでしょう。
なお、図面管理システムを詳しく知りたい方は、ぜひこちらよりカタログをダウンロードください。
3. 図面管理システム×発注管理システム連携で発注ミスをさらに削減
図面管理システムだけでなく、発注管理システムとも連携することで、誤った部品の発注リスクをより軽減できます。
ここでは、発注管理システムの概要や具体的な連携方法、効果を詳しく解説します。
- 発注管理システムの概要と機能
- 図面管理システムと発注管理システムの連携による効果
- 図面管理システムと発注管理システムの連携方法
それぞれ見ていきましょう。
3-1. 発注管理システムの概要と機能
発注管理システムは、製造業における部品や材料の発注業務を効率的に管理するためのシステムです。
おもな機能を以下にまとめました。
基本機能 | 詳細 |
---|---|
発注情報の登録・更新・検索機能 | 発注情報を簡単に登録・更新・検索でき、必要な情報に迅速にアクセスできる |
在庫管理機能 | 在庫状況をリアルタイムで把握し、必要なタイミングで適切な量を発注できる |
納期管理機能 | 発注品納期を管理し、納期遅延を防ぐためのスケジュールを調整する |
自動発注機能 | 事前に設定した条件に基づいて、自動的に発注でき、手動によるミスを減らす |
発注履歴の管理機能 | 過去の発注履歴を管理し、発注内容の確認や分析をする |
3-2.図面管理と発注管理のシステム連携により実現できる4つのポイント
図面管理システムと発注管理システムのデータ連携は基本的には、APIを利用して接続します。以下に図面管理システムと発注管理システムを連携することで、実現できるポイントを4つにまとめました。
ポイント1:図面情報の参照
発注管理システムで発注する際に、最新の図面情報の参照が可能に
ポイント2:通知機能の設定
図面管理システムで図面が更新されると、発注管理システム内の関係者に自動的に通知
ポイント3:データ整合性のチェック
発注管理システムで発注する際に、図面情報と発注情報の整合性をチェック
ポイント4:定期的なメンテナンスとアップデート
両システムの連携部分が正常に動作しているかを定期的にチェック
なお、API連携以外にEDIなどの方法を用いることも効果的です。EDIを利用することで、異なるシステム間でのデータ交換が標準化され、さらにスムーズな連携が実現できます。
3-3.図面管理システムと発注管理システムの連携による3つの効果
図面管理システムと発注管理システムを連携することで得られる効果を3つにまとめました。
効果1:誤った部品の発注を防ぐ
図面が変更された場合、変更情報を発注管理システムから参照することで、正しい図面をもとに発注できます。さらに、発注プロセスの自動化により、手作業によるデータ入力ミスを減らせます。
効果2:関係者間の行き違いを防ぐ
図面情報の変更や発注状況など、関連する作業者に通知します。これにより、古い情報に基づく誤発注や設計者と発注者の行き違いの防止が可能です。
効果3:最適なタイミングで発注可能
発注管理システムと連携することで、発注履歴や在庫状況、発注状況の進捗などの把握が可能に。情報が一元管理されるため、必要な部品を適切なタイミングで正確に発注できます。
上記の効果から、最終的には誤製造防止につながります。
4.図面管理システム×発注管理システム連携は外注がおすすめ!NAZCA5 EDMにお任せください。
自社で図面管理システムと発注管理システムをすべて開発・連携させるのは、多くの時間とコストがかかり、専門知識も必要です。そのため、ITおよび製造業に詳しいベンダーに外注することをおすすめします。
新明和ソフトテクノロジが提供する「NAZCA5 EDM(ナスカファイブ・イーディエム)」は、製造業が本当に使いたい機能を厳選した図面管理システムです。使いやすさと柔軟さを兼ね備えています。
製造業への支援で蓄積してきたノウハウを生かし、各社様の状況に応じた適切なご提案をします。また、導入に向けた各種サポートもお任せください。
また、お客様の予算に合わせて、セルフ導入プラン、おまかせ導入プラン、フルカスタムプランの3つのプランをご用意しています。
発注ミスの削減には、図面管理システムとの連携が重要です。
ぜひ「NAZCA5 EDM」の導入をご検討ください。失敗のない導入をお手伝いいたします!